Get Your Copilot
Create an AI Chatbot for Light Industries
Cut downtime, boost productivity, and improve communication across departments with our Copilot.live chatbot that helps you run a leaner, smarter factory operation.
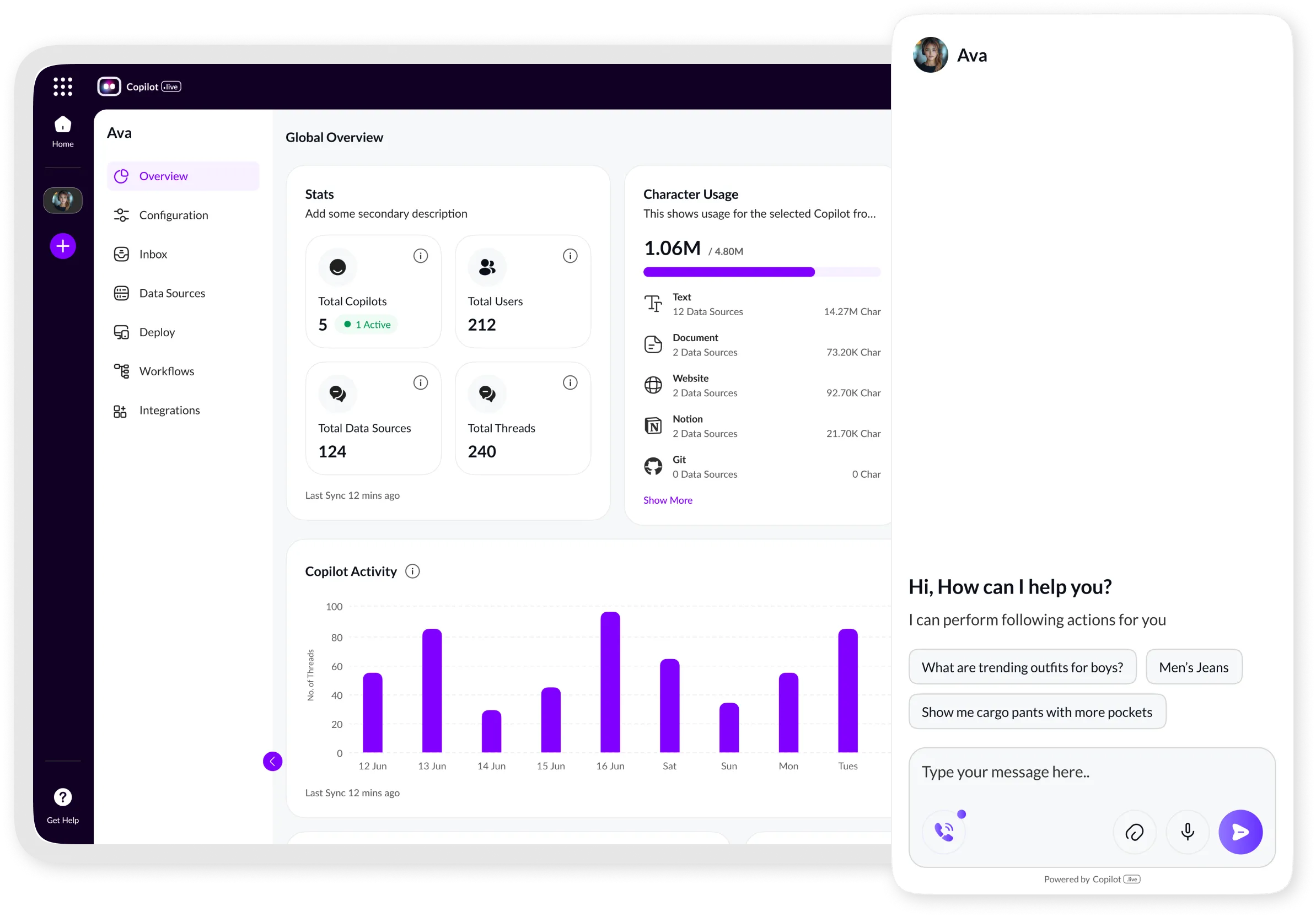
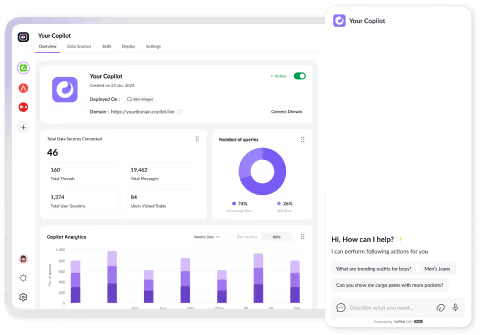
Create an AI Chatbot for Light Industries
Cut downtime, boost productivity, and improve communication across departments with our Copilot.live chatbot that helps you run a leaner, smarter factory operation.
Build an AI assistant in 3 minutes
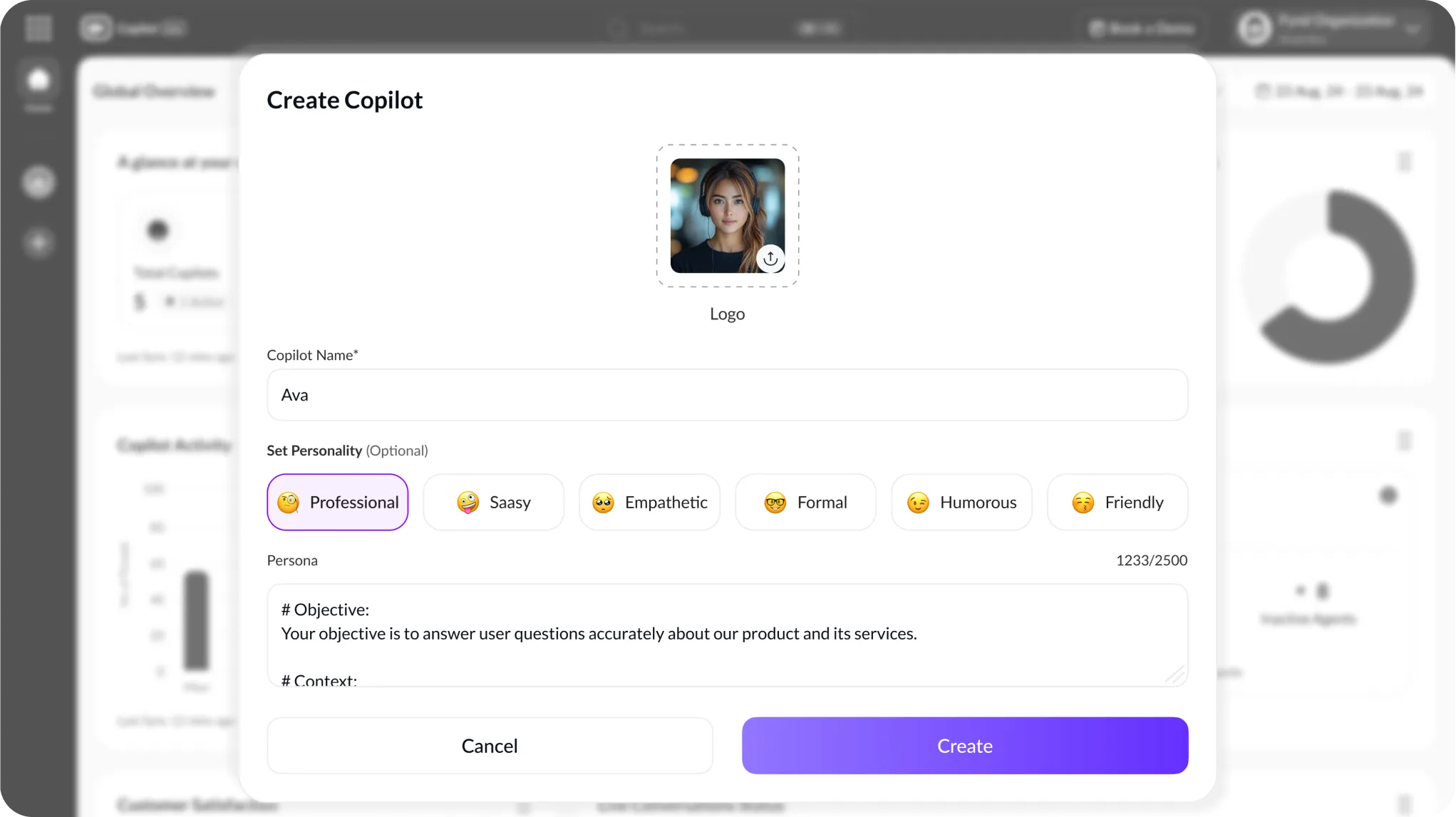
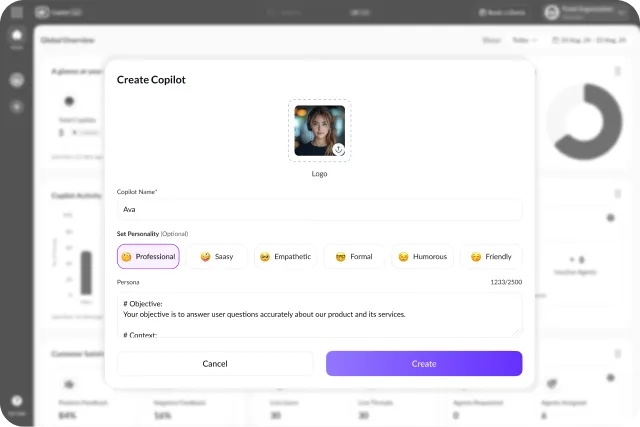
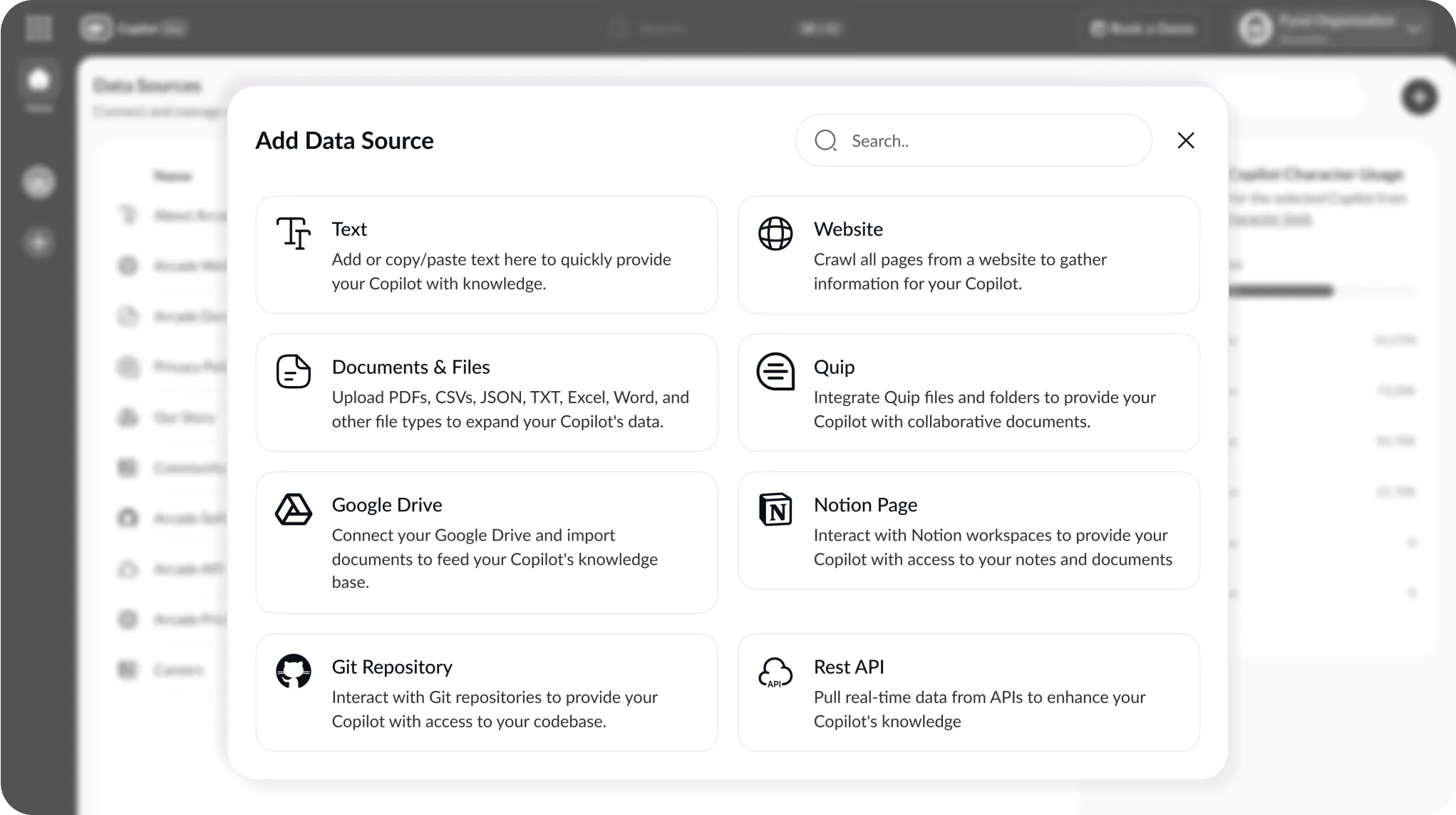
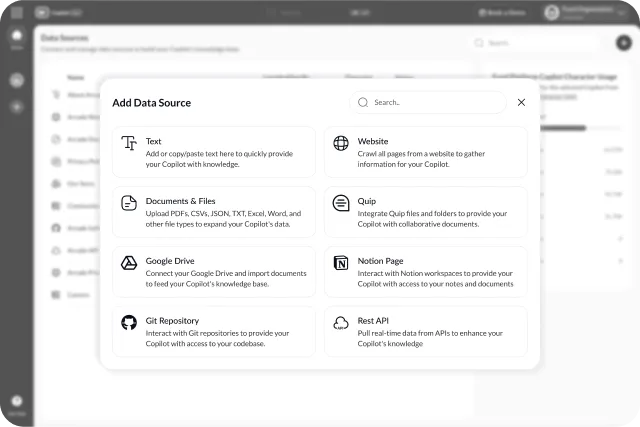
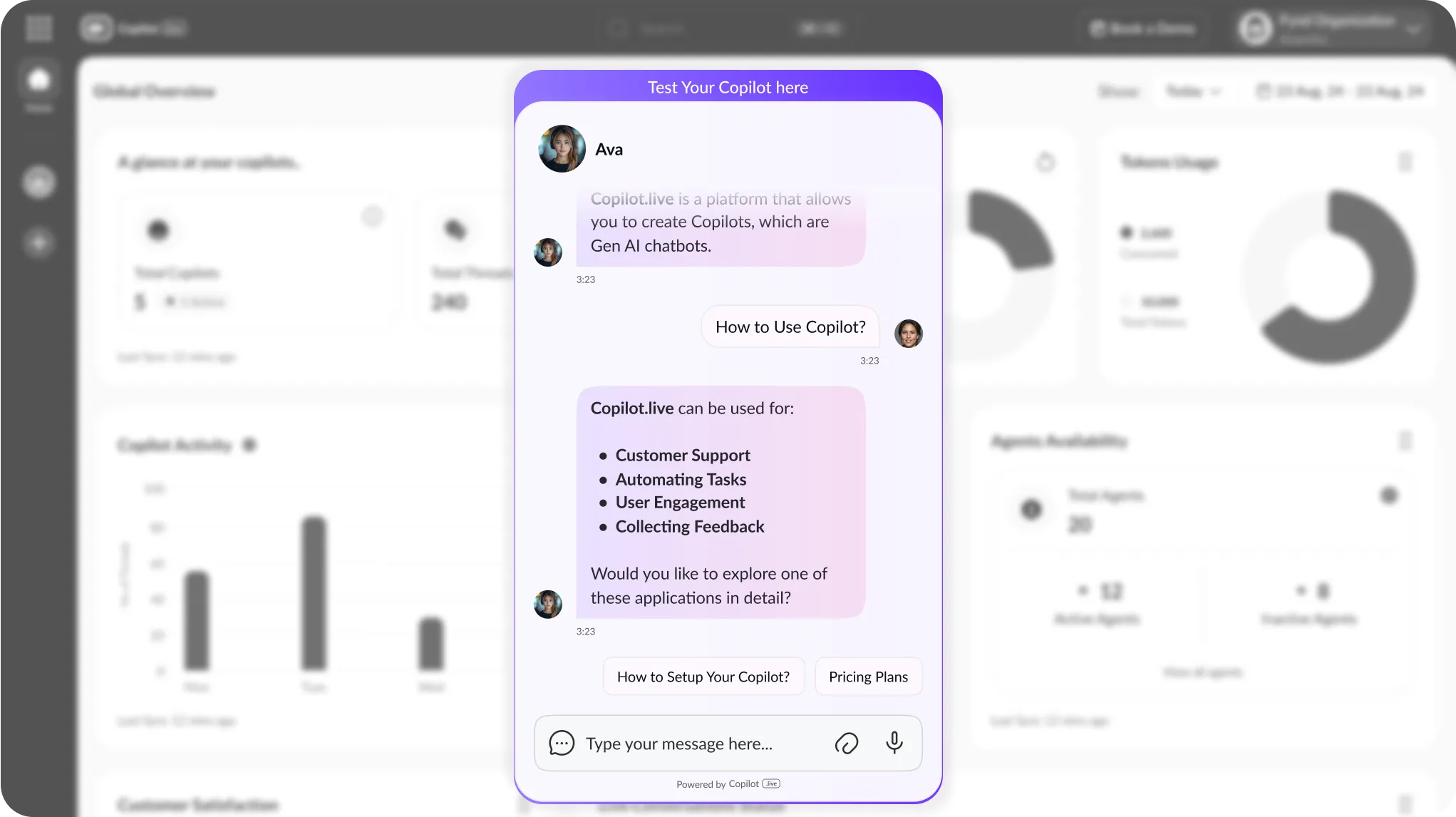
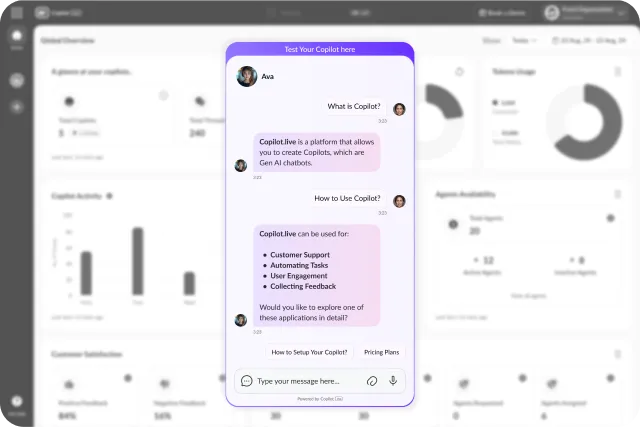
How to create a chatbot for light industries?
Sign up for free
Visit the website Copilot.live and click on the “Sign up” button. Create your profile by inputting your name and email ID along with a new password. For quicker account creation, you can use a Google or Apple ID.
Customize the chatbot
After creating your account, proceed to customize the chatbot as per your brand persona. The name, colour, style, and tone of the chatbot can be set as per business requirements.
Add data sources
Now, hit the button “Add data sources”. You can add multiple sources such as files, databases, and websites. Chatbots can be fed updated information to ensure that the responses are current.
Test & deploy
You can also train and test the chatbot yourself. After deploying the bot on your system, you can further add it to your website or integrate it with other business tools, provided you are satisfied with the responses.
.png)
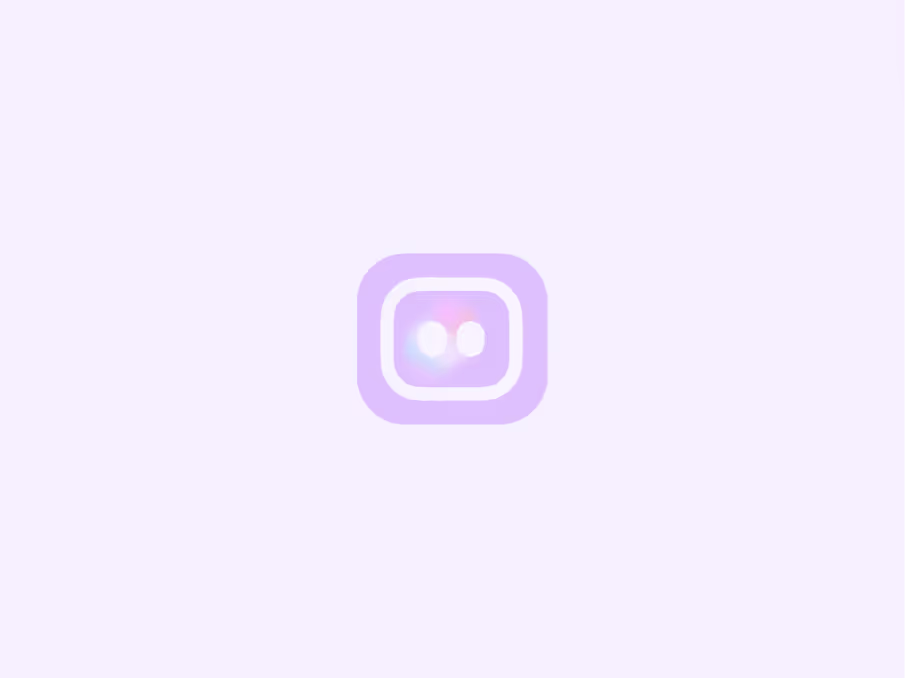
What is a chatbot for light industries?
Light industries chatbot is an intelligent virtual assistant that will help factories and production units operate more effectively. It can respond to frequently asked questions, distribute important updates, and help direct workers through their day, all via a simple chat interface. Whether you’re looking to look up shift schedules, report an issue with a machine, or see if a part is in stock, the chatbot is your crew’s always-on resource for enabling their success.
Unlike general-purpose chatbots, this one is designed specifically for the needs of light manufacturing — things like electronics, textiles, consumer goods, and packaging. It can tap into existing systems to retrieve real-time data, remind teams to do safety checks, and even help onboard new staff.
The best part? It runs on mobile and could also potentially even scale across multiple languages, and is intuitive enough for every shop floor worker to use. In short, it's like having a smart tailoring assistant when you need it, all designed to make factory work easier and faster.
Why is there a need for a chatbot for light industries?
To cut down time for mundane tasks
Workers and managers tend to waste significant time answering the same questions, such as when their shift starts, inventory levels, or how to report a machine problem. A chatbot takes care of these in seconds, so the team can get on with their more valuable work without constant interruptions and delays.
To better communicate on the floor
In noisy factory environments, messages can easily become lost or misinterpreted. A chatbot provides all people with one source of truth, without bias, whether it’s for safety advisories, campaign dates, or instructions. This is useful not just because it prevents confusion, but also because it keeps everyone on the same page.
To support deskless employees all day long
Most light industry workers are not sitting at desks — they are on the move. They can speak directly to a chatbot on their phone or tablet, and it gets them the knowledge they need, when and where they need it, for example, SOPs, HR info, or machine manuals, without having to find the correct person.
For easier training and onboarding
New hires are teeming with questions. A chatbot can walk them through tasks, describe safety guidelines, and provide answers to the frequently asked questions that come with any new job, helping them ramp up more quickly. This takes the load off managers and provides equal training to all.
.png)
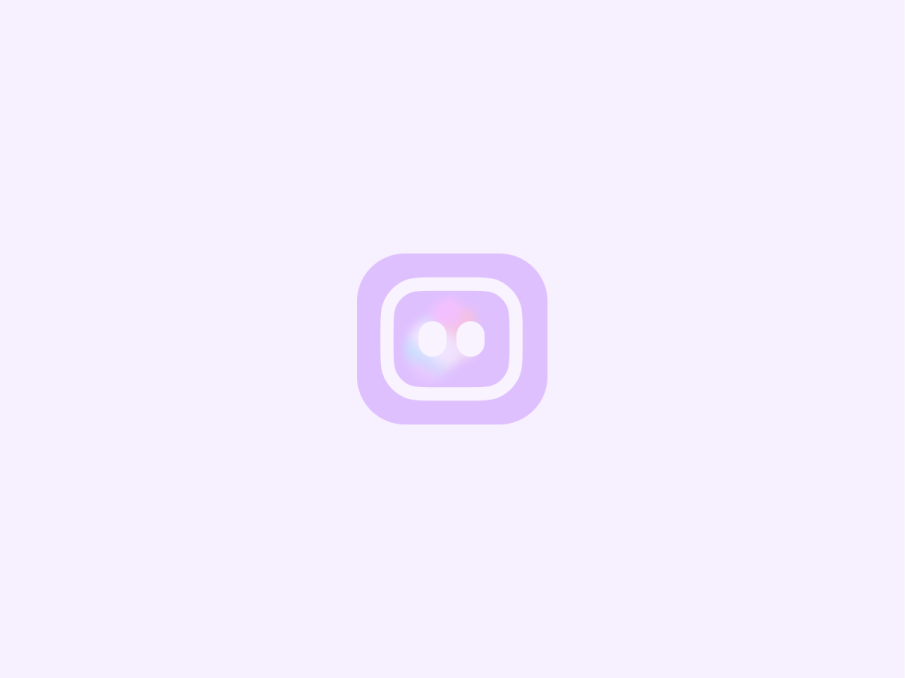
Who needs a chatbot for light industries?
A chatbot for light industries assists factory owners and the entire plant management cycle, including supervisors and HR teams, in addressing issues of communication bottlenecks, delays, and information silos. In light industries such as textiles, packaging, and electronics, answering basic queries related to shifts, machines, and inventories is a persistent problem for workers. Supervisors experience frequent disruptions, and the HR teams are overwhelmed with a plethora of standardized questions.
Chatbots provide prompt access to an organization's information repository and disseminate data that can be relied upon by operators and workers on the shop floor. This improves information clarity and accelerates reporting while streamlining the overall information retrieval system. Moreover, the chatbot can also help with instructing new workers on the safety procedures or notifying maintenance after a breakdown. The benefits are undeniably instant, and operational effectiveness is greatly enhanced.
Key benefits & features of Copilot.live chatbot for light industries
Transform how your factory communicates with Copilot.live chatbot that works across departments to reduce delays, errors, and manual follow-ups.
Instant answers, anytime
The chatbot provides quick and instant responses to frequently asked questions, such as shift times, the status of stock, or how to report issues. No supervisor needs to be called or a paper to be searched. This is a time saver and prevents backlogs, etc. from stalling everything.
Smart workflow support
Copilot.live chatbot, can take workers through daily tasks, SOPs, and even troubleshoot simple issues the machine may experience. Because it offers line-by-line assistance, it minimizes errors and ensures that jobs are done the same way every time, even by new or less experienced workers.
Live reporting and alerts
Workers can report problems like machine breakdowns or low stock via the chatbot itself. The right team will be instantly alerted, and problems will be solved more quickly.” You also receive notifications and updates, so managers never have to chase information.
Easy access, any device
It doesn’t matter if someone is on a phone, tablet, or shop floor terminal; the chatbot is accessible to all. It also has support for multiple languages, so it can be helpful across a diverse workforce. By doing so, more people have the info they need when they need it.
Copilot.live chatbot for light industry use cases
Replying to employee questions
Workers often have straightforward questions, be they about shift schedules, the amount of leave left, or safety procedures. Instead of needing to appeal to HR or a manager, they can simply ask the Copilot.live chatbot. It offers quick, accurate answers on demand, while keeping teams on the same page and reducing the back and forth that can gum up the wheels of commerce.
Prompt communication of equipment problems
When a machine goes down, time is of the essence. With Copilot.live chatbot, workers can report problems from the shop floor. If there is one, the chatbot logs the issue and communicates it in real time to the maintenance crew — no paperwork or hunting people down. This translates into faster repairs, less downtime, and more production.
Onboarding new employees
Team members new to the kitchen often need help learning procedures and safety precautions. Copilot.live chatbot acts like a coach who's there to answer questions, share SOPs, and train them on tasks. It enables new hires to more quickly become acclimated to their role without requiring the type of constant supervision that often results in hit-or-miss onboarding.
Providing updates & alerts on the situation
Managers can use Copilot.live chatbot to transmit quick updates, like shift changes, emergency alerts, or policy changes. Now everyone sees the same message at the same time, right on their device. This keeps the team on the same page, minimizes miscommunication, and prevents important information from falling through the cracks.
Inventory & supplies tracking
Wondering if a part is in stock or when supplies are on the way? Just ask the chatbot for light industries. Copilot.live chatbot, integrates with your inventory system to provide real-time responses. It prevents delays from missing parts and allows workers to concentrate on getting the job done, rather than searching stock by hand.
Giving instructions for your task
Employees can also request from the chatbot how to do certain tasks or use certain machines. It can provide step-by-step instructions with photos or videos for something straightforward. This is to make sure work is done correctly, safely, and quickly. It is also obligatory as the tasks involved are typically elaborate and appear rarely.
.png)
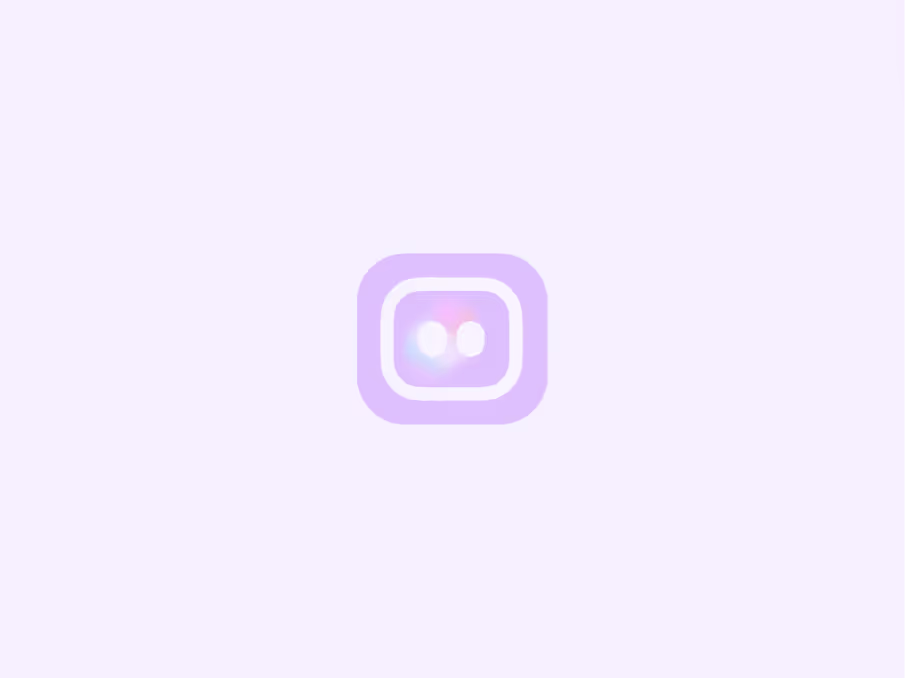
Factors to consider for building a chatbot for light industries
When creating a chatbot for light industries, you must consider more than just question-answering. The chatbot will need to support the staff and processes on the factory floor.
Here are some of the key factors to consider:
- Ease of Use: It has to be mobile-friendly and easy for anyone (literally) to use, even with basic technology proficiency.
- Multilingual: A lot of people do not speak the same language. So, multilingual support is an essential feature.
- Integration with existing systems: You can connect the chatbot to HR, inventory, and maintenance tools.
- Offline support or poor connectivity mode: Many shop floors have slow internet. The chatbot must still work reliably in poor internet connections.
- Role-based access: Each team has its own info needs. So, make sure that it’s tailored.
Picking the right features means your chatbot is helpful instead of just another thing in the way.
The future of the light industries chatbot
The future of chatbots in light industry seems bright. Today, factories and production lines struggle with common issues, such as bad communication, slow reporting, and a lack of real-time data. Workers wait to receive answers, new employees require constant guidance, and managers find it increasingly difficult to keep up with everything happening on the floor.
As chatbot tech gets better, that will all be easier to deal with. Chatbots in the future will be much more intelligent, capable of voice assistance, better language comprehension, and integrated more deeply with factory systems. They will be able to see patterns, anticipate equipment breaking down, and avoid failure before it happens.
AI chatbots will also help managers to make decisions faster by providing real-time data pulled from machines, stock systems, and HR tools. They will act as digital assistants, remember previous engagements, and get better over time. That means fewer delays, less waste, and more cohesive, productive teams.
Additionally, chatbots will increasingly become the fabric stitching together humans, machines, and processes as factories embrace automation and intelligence. That means the production process runs more smoothly, safely, and productively than it used to.
.png)
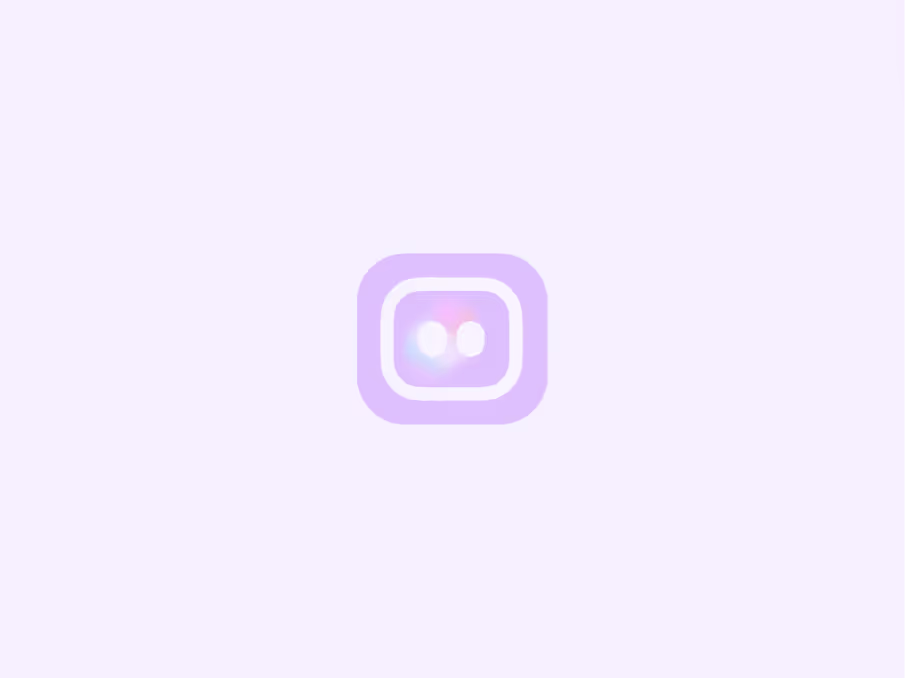
Frequently Asked Questions
You can reach out to us in case of any queries, feedback, or suggestions via [email protected] or read below.
A. It’s a smart virtual assistant that helps workers and managers in factories by answering questions, sharing updates, and guiding tasks, right from a phone, tablet, or computer.
A. It can assist with shift info, report machine issues, guide workers through tasks, and send important alerts. It saves time and improves communication between teams.
A. Yes. A good chatbot can connect with tools like HR software, inventory systems, and maintenance logs to give real-time answers and updates.
A. Absolutely. It’s built for non-desk workers and designed to be simple, mobile-friendly, and even multilingual, so everyone can use it easily.
A. Yes. The chatbot is always on, so your team can get help anytime, whether it's during a shift change, overnight production, or weekends.
A. Yes. The chatbot can guide new workers through safety rules, procedures, and FAQs, making onboarding smoother and faster without needing constant supervision.